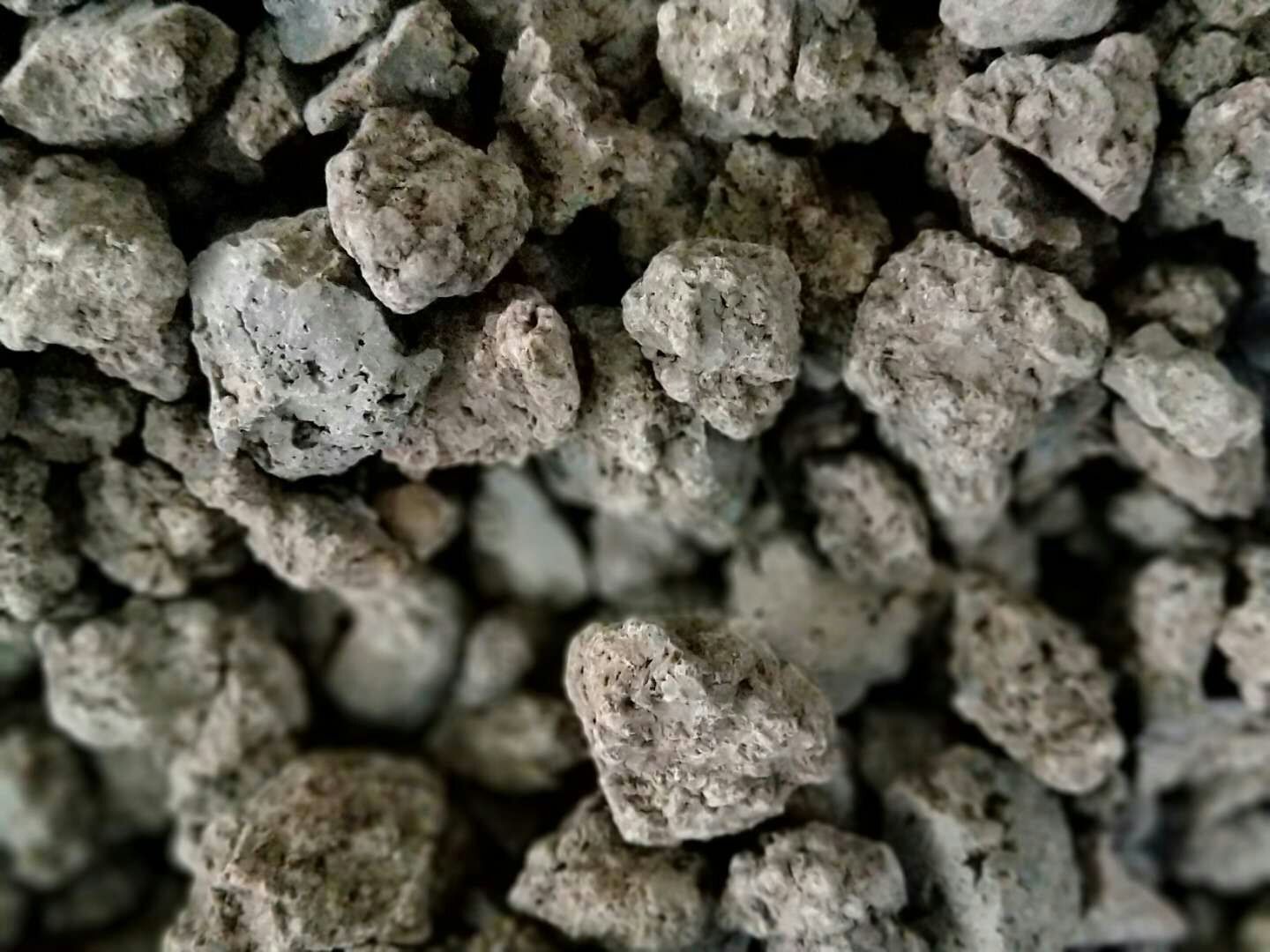
Calcium AluminateThe Refining Slag refers to a technique in which the raw materials are mixed at a certain ratio and particle size, heated at a temperature lower than the melting point of the raw materials, and the raw materials are sintered together and then broken into particle sizes. The main components are CaO-CaF2 group, CaO-Al2O3 group, CaO-Al2O3-SiO2 group, and the form of refining slag mainly includes sintered type, pre-melted type and mixed type.
The composition of the sintered Refining Slag is more uniform, stable, and the melting speed is faster, but the cost is relatively increased, and since the density of the sintering slag is small, there are many pores, which easily cause inhalation in the refining process.
Pre-refined Refining Slag refers to refining slag used for steelmaking after mixing raw materials in a certain proportion and using high temperature in a special equipment to melt the raw materials into a liquid state at a temperature higher than the melting point of the slag system, and then cooling and crushing. Pre-melted Refining Slag has high purity, uniform chemical composition, stable phase, low melting point and fast slag forming speed, which can greatly shorten the refining time and can be directly used for slag washing in converter ladle tapping process to improve the cleanliness of molten steel. And no fluorine or a small amount of fluorine, reducing lining erosion, effectively reducing the pollution of fluorine to the environment. Because the pre-melted refining slag has a compact structure, does not absorb water, is convenient for storage and transportation, is not powdered, and does not volatilize, can significantly reduce dust pollution of steel plants, but the production cost is high.
In the metallurgical process, the slag composition has a very important influence on the cleanliness of molten steel. The high oxidizing slag that enters the ladle after the tapping of the converter will continue to continuously transfer oxygen to the molten steel due to the high content of unstable oxides such as FeO and MnO, which seriously affects the yield of aluminum and the cleanliness of the molten steel. Causes nozzle clogging and sheet surface quality defects.
- Prev:None;
- Next:Deoxidizer
-
Deoxidizer
-
Ferro Silicon
-
Silicon Carbon Alloy
-
Cored Wire
-
High Carbon Ferro Silicon
-
Silicon Briquette
-
FeTi Cored Wire
-
Silicon Metal Powder
-
Seamless Metal Calcium Cored Wire
-
Carbon Additive
-
Ferro Silicon Powder
-
Ferro Silicon Briquette
-
Silicon Carbon Alloy Powder
-
High Carbon Silicon Briquette
-
Composite Deoxidizer
-
Silicon Aluminum Composite Deoxidizer
-
Silicon Calcium Composite Deoxidizer
-
CaFe Cored Wire
-
Solid Compound Calcium Cored Wire
-
Ferro silicon magnesium
-
Sulfur Cord Wire
-
Silicon Carbide Deoxidizer
-
Silicon Calcium Manganese Deoxidizer
-
Silicon Calcium Cored Wire
-
Silicon Carbon Briquette
-
Silicon Barium Calcium Cored Wire
-
Silicon Barium Cored Wire
-
Silicon Barium Alloy
-
Silicon Aluminum Calcium Deoxidizer
-
Aluminum Cored Wire
-
Calcium Metal Cored Wire
-
Silicon Carbon Alloy
-
Silicon Calcium Barium Alloy
-
Silicon Aluminum Alloy Deoxidizer
-
Green Silicon Carbide
-
Ferro Silicon Aluminum Alloy
-
Silicon Calcium Alloy
-
Silicon Aluminum Manganese Alloy
-
Black Silicon Carbide
-
Manganese metal ingot
-
Silicon metal
-
Manganese flake
-
Low Carbon Silicon
-
Calcium Aluminate